ldpe autoclave technology|ldpe for extrusion : store Low density polyethylene (LDPE) resins from LyondellBasell are thermoplastics made from the polymerization of ethylene in autoclave or tubular reactors at very high pressures. Unlike low-pressure polymerization technologies, high-pressure polymerization allows the co-polymerization of ethylene with polar comonomers, such as vinyl acetate or . This manual covers complete instructions for the installation, operation, and nor-mal care of the M9 / M11 UltraClave™ Steam Sterilizer. It is intended that this manual be used by any .
{plog:ftitle_list}
Find your steam sterilizer easily amongst the 896 products from the leading brands (SUGOLD, CARLO DE GIORGI, FAITHFUL, .) on MedicalExpo, the medical equipment specialist for your professional purchases.Statistics for the 2024 Steam Autoclave market share, size and revenue growth rate, created by Mordor Intelligence™ Industry Reports. Steam Autoclave analysis includes a market forecast outlook 2029 and historical overview. Get .
offers high-pressure tubular and autoclave process technologies for the production of low density polyethylene (LDPE) and ethylene vinyl acetate (EVA) copolymers. The Lupotech T process is .LDPE, produced by the high-pressure polymerization of ethylene, is an important commercial product used in film, paper coating, injection molding, and wire/cable insulation. Autoclave is a single source for the design and supply of polyethylene production reactors. Autoclave also supplies associated equipment like Separator Vessels, Catch Pots and Pulsation Bottles for .
For tubular processes, estimates are developed for LDPE and EVA (18% VA), while for autoclave processes, estimates are developed for LDPE and EVA (18% VA and 28% VA). In each region, the technology (tubular versus . The ExxonMobil Autoclave technology also exists with a Tubular Tail connected to the primary autoclave reactor. Therefore, a Tubular Tail unit is available in the list of units when such a Tubular Tail technology is designed. . from the tubular process is typically higher in molecular weight and has more short chain branches than LDPE from .Low density polyethylene (LDPE) resins from LyondellBasell are thermoplastics made from the polymerization of ethylene in autoclave or tubular reactors at very high pressures. Unlike low-pressure polymerization technologies, high-pressure polymerization allows the co-polymerization of ethylene with polar comonomers, such as vinyl acetate or .
Low-density polyethylene (LDPE) resins are used to produce a range of general-purpose and high-performance applications, which include blown and cast film, extrusion and coating, and rotational and injection molding. ROTTERDAM, Netherlands, Aug. 25 /PRNewswire/ -- LyondellBasell Industries announces the launch of Lupotech A technology for the production of specialty low density polyethylene (LDPE) and ethylene vinyl acetate (EVA) products. This high-pressure autoclave process technology is optimized for the manufacture of advanced products with demanding .POLYETHYLENE PRODUCTION TECHNOLOGIES PE Polymerization Techniques The route to PE falls into two categories: 1. High pressure polymerization • Produces LDPE • Operating pressure ranging from 1000 to 3000 barg • Operating temperature from 80 to 300 °C • Autoclave or tubular reactor • Free radical catalysts using initiators (peroxides)
From plastic bags to containers, LDPE's ease of processing and durability make it an essential in modern manufacturing. SCGC™ LDPE is a low-density polyethylene resin produced by an autoclave process, a technology developed by ICI Co., Ltd., suitable for extrusion coating and lamination applications used in flexible packaging and aseptic box. The chapter presents a hands-on workshop for simulating an autoclave high-pressure (HP) LDPE process. It also presents an effective methodology for estimating the kinetic parameters based on plant data in the development of simulation and optimization models for commercial polyolefin processes involving free radical polymerization. Another .The first LDPE/EVA (Low Density Polyethylene / Ethylene Vinyl Acetate) autoclave process was introduced in 1938. In this type of application, a mix of pressurized ethylene gas and catalysts is stirred at high temperature in a vessel. The stirrer is turned by an electric motor which is in line with the vessel.
LDPE autoclave process LDPE is produced either in a tubular reactor (PFTR, LDPE tubular process) or in a high-pressure, continuous stirred tank reactor (CSTR, LDPE autoclave process). In both process designs the very high pressures require very special, thick-walled equipment and fatigue is a major design aspect for the applied pumps and compressors. In the LDPE .
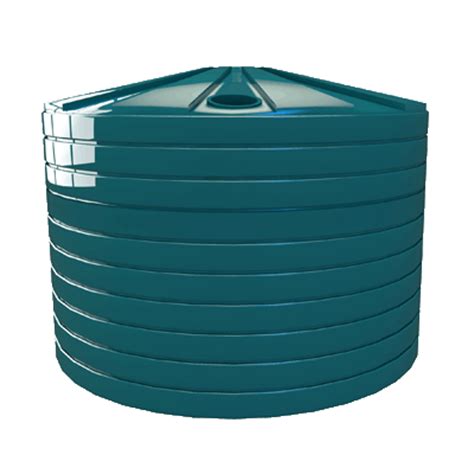
qenos autoclave ldpe
In general autoclave LDPE outperforms tubular LDPE with respect to neck-in. The draw down limit for tubular LDPE on the other hand is higher than for autoclave. The work presented here provides technical details of the benefits of blending tubular LDPE with autoclave LDPE for extrusion coating applications. For a lab scale line, it is shown that at 30 to 50% tube resin . Process Summary. The Autoclave Reactor Polymerization of Ethylene is a non-catalytic Process that operates with Organic Peroxides as Radical Initiators at an operating pressure from 1,300 to 2,000 bar and a Reactor Temperature of up to 310°C. The aim of the present work is the development of a practical model for an industrial high-pressure polyethylene plant. The reactor considered in this work is the adiabatic slim type autoclave .Detailed models of industrial Low-density polyethylene (LDPE) autoclave reactors have been built by integrating several advanced modeling concepts: (a) An advanced thermodynamic model based on the Statistical Association Fluid Theory (SAFT) γ-Mie Equation of State, which represents molecules as chains of distinct functional groups [1-3]. .
We hold the technology for the ICI LDPE processes, and can provide support and assistance with all operational ICI plants. We are also an approved . 25% Capacity Increase for LDPE/EVA plant using ICI autoclave technology Our range of activities included: • Feasibility study and budget cost estimate, followed by ±10% projectThe extrusion coating market (EC) is still dominated by autoclave LDPE. As described in the literature this is a consequence of the typical molecular mass distribution (broad + long chain branching) of the autoclave resins, . This difference in MMD can be explained by comparing the technology of a tubular reactor with an autoclave. A tubular .
Uhde HPT manufactures full function tested autoclave reactor systems including steel construction design as ready-to-use plants including all accessories like e.g. motors, agitators, bearings, power electrodes, flushing pumps, rupture discs, hydraulic top and bottom cover and clamp handling devices, vibration measurement, various special maintenance tools for reactor .
Lupotech A –Autoclave Polyethylene Technology Autoclave process for the production of LDPE and very high EVA copolymers (up to 40%) Autoclave process for the production of LDPE and very high EVA copolymers Well-proven technology 44 reactors in operation 1.8 million tons licensed capacity 4 licenses granted in 2013 (4 x 100KTA) 51. POLYETHYLENE PRODUCTION TECHNOLOGIES Exxon Mobil (Tubular/Autoclave) Features • The tubular reactors operate at pressure up to 3,000 bar, where Autoclave reactor operates below 2,000 bar. • MI range: 0.2 – 150 • Density range: 0.912 – 0.935 • Reactor turn down ratio: 50% • Short residence times.2x 400kta LDPE USA 400kta LDPE United Kingdom 350kta LDPE Saudi Arabia 300kta EVA China New Build ECI Group has worked closely with all major licensors of high pressure tubular and autoclave processes and specialist equipment vendors, and can offer you impartial advice for your plant. We will work with you at all stages of the project life .of low density polyethylene (LDPE) and ethylene vinyl acetate (EVA) copolymers. The Lupotech T process is the leading high pressure tubular reactor technology for the production of LDPE and standard EVA, while Lupotech A is the high-pressure autoclave reactor process technology for the production of specialty LDPE, EVA copolymers with very
ExxonMobil™ LDPE resins are suitable to produce a large variety of general-purpose applications along with being excellent blend partners in high-performance applications, which include blown and cast film, extrusion coating, rotational and injection molding.ECI Group licenses proprietary autoclave and hybrid technology for high pressure polyethylene. Our technology is developed from the well-proven ICI autoclave and has been optimized for modern materials, design techniques, industry standards, and best practises.autoclave technology. The quality of PE mainly depends on density and degree of branching. . In LDPE, typically 10-40 SCB and 0.3-03 long chain branching (LCB) exists respectively per thousand .LDPE Technology 2010 Előadó: Csernyik István. 2 Content . LDPE - - Autoclave Process. Initiators (Peroxides) Autoclave reactor Secondary compressor Primary 280 bar 250 C HP separator Wax separator 0,5 bar 250 C LP separator Extruder. Ethylene. Oil .
ALCUDIA® 2221F is a low density polyethylene grade, produced by high pressure autoclave technology, suitable for thin blown film applications. This material offers easy processability and good balance of mechanical and optical properties. It contains antioxidant additives. TYPICAL APPLICATIONS - Thin shrink film - Thin pouches - General packaging film - Bubble film - .
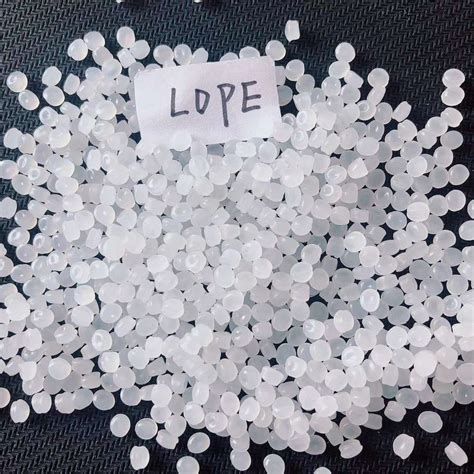
ldpe for extrusion
Here is an item that you should use regularily in order to verify that your sterilizer autoclave did achieve the temperature desire. This is a themometer range is between 150?F to 350?F (65?C to 177?C). Click here .
ldpe autoclave technology|ldpe for extrusion